How Do Brake Discs Work?
22nd November 2019
the disc brake system
The electric revolution may still be in its infancy, but it’s undeniable that fossil fuel-based engines are on borrowed time. However, whether they’re battery powered or fuel cell-based engines, the future greener vehicles will still need to prioritise passenger safety for any commercial or mass produced vehicles. We can then safely assume that the braking system will be unchanged for the foreseeable future, until a more revolutionary system can be produced of course.
The majority of cars produced today utilise the disc brake system; drums are still used by some manufacturers, however their effectiveness pales in comparison to the disc brake.
The disc braking system involves many different components, but at its most basic function, the system consists of a disc/rotor, a brake calliper and brake pads. When the brake pedal is applied, brake fluid creates pressure and squeezes the brake pad against the rotor and creates friction. This friction slows the rotation of the wheels and the car itself. Simple?
There is obviously a little more to it than that, with each component engineered to maximise breaking performance.
Disc/rotor
The disc or rotor is the largest part of the disc brake system and is fixed to each wheel, via the holes on the front of the hub (pictured). Discs usually consist of cast iron, but each will have a specific mix of metals based on the vehicle type and performance needs. The disc is the contact surface for the generation of friction in the braking system, so it needs to be able to withstand immense pressure and heat.
Due to the intense heat applied to the disc during the process, the majority are ventilated, optimising the flow of cold air during braking. This stops the disc from becoming too hot, potentially damaging the disc or other parts of the system. The vent design is specific to the car manufacturers request and can take upon a variety of different shapes and types. Another method used to increase air flow, is to machine grooves on the exterior of the disc. Much like the vents, these increase surface area and optimise air flow to the disc and the braking surface directly.
You can read more about the different types of brake discs, vent and groove designs here.
Brake Caliper
Brake calipers are the clamp like component that fits over the disc. Their main function is to push the brake pads into the disc, and they do this via pistons and hydraulic brake fluid.
Inside the calipers are pistons, which have the brake pads attached to them. When we put our foot on the brake, pressurised fluid is sent to the pistons and they push against the pads, which contacts with the disc surface.
You can read more about the brake caliper here.
Brake pads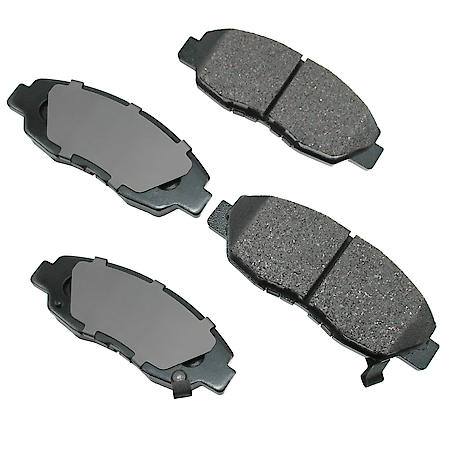
The final primary component of the brake disc system is the brake pad - the pad is a steel backed plate, with a friction-based material bound to their surface. Usually there will be two housed within the brake caliper, attached to the pistons with the friction surface directed at the disc.
Sufficient friction material on the pad is essential, as the disc may become damaged and worn down without the correct contact during the braking process. Brake pads can come in a variety of different materials, dependant on the type of vehicle needed to be stopped.
In order to stop a vehicle weighing in excess of 1000kg, the pads need to be able to withstand extreme heat and friction. Surprisingly there is a large variety of different materials used for brake pads, all considerably resistant. The most popular material and likely to be on your own car, is a metallic brake pad. They’re a blend of different metals; commonly made of iron, copper, steel and graphite.
Metallic brake pads are heavy though and if speed is the name of the game, then a more lightweight material is needed, such as ceramic. You can read more about the different brake pad types and materials here.
Mat foundry group
At MAT Foundry Group we specialise in the casting and machining of brake discs and brake calipers, two essential components of the disc braking system. Our highly skilled process and development engineers support both original equipment manufacturers (OEM) and aftermarket customers with research and development across the globe.
Our sister company MAT Friction Group serve the passenger, commercial, and heavy-duty vehicle markets with a variety of braking components including pads, shims and back plates, and brake shoes and linings.